飞轮壳连接着发动机和离合器壳,是传动系中的关键部件。随着工况环境的要求越来越高,将会加速飞轮壳的损坏。结构设计的不合理、生产工艺问题及安装调试不当等都是造成飞轮壳损坏的主要原因。
根据福州奥特帕斯工业有限公司提供的飞轮壳模型及归纳的裂纹常发生位置,我们将通过有限元模拟分析飞轮壳出现裂纹的原因,以提供结构改进方案的依据。
1 力学模型
1.1飞轮壳结构原理分析
机器在运行过程中,飞轮壳的断裂是来自发动机、离合器传系和机座的反作用力、振动及弯矩相互作用的结果。飞轮壳受力的短时间内可认为是静态的,因此,本分析将对飞轮壳结构进行静力学分析以找到合理的断裂原因。有限元模拟主要分析飞轮壳受力来自于机座和传动系两种可能情况。
1.2飞轮壳结构的有限元模型
设置飞轮壳的材料物理参数,添加载荷及边界条件。载荷分为传动系施力和机座施力,并且分别在两种载荷下设置5种工况。
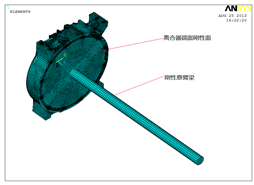
图1-1 飞轮壳-离合器端面施力结构示意图
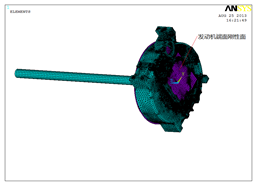
图1-2 飞轮壳-发动机端面施力结构示意图
工 工况汇总
| 工况序号
| 载荷条件
|
传动系施力
| 工况1
| 发动机端部及左机座全约束固定;刚性悬臂梁施加fx=1.0×105N
|
工况2
| 发动机端部及左机座全约束固定;刚性悬臂梁施加fy=1.0×105N
|
工况3
| 左机座全约束固定,发动机端释放;刚性悬臂梁施加fy=1.0×105N
|
工况4
| 发动机端部及左机座全约束固定;刚性悬臂梁施加fx=1.0×105N,发动机端施加fx=1.0×105N
|
工况5
| 发动机端部及左机座全约束固定;在离合器连接的每个螺栓上均布X正方向的力,力值总和为1.0×105N
|
机座施力
| 工况1
| 发动机端部固定;左上、下机座均施加fz=1.0×105N
|
工况2
| 发动机端部固定;左上、下机座和右上、下机座均施加fz=1.0×105N
|
工况3
| 发动机端部固定;左上、下机座均施加fz=2.0×105N,右上、下机座均施加fz=1.0×105N
|
工况4
| 发动机端部固定;左上、下机座均施加fz=1.0×105N,右上、下机座均施加fz=-1.0×105N
|
工况5
| 发动机端部固定;左上机座和右上机座均施加fz=1.0×105N,左下、和右下机座均施加fz=-1.0×105N
|
2有限元网格模型
飞轮壳结构复杂,划分六面体网格不易实现。本分析采用4节点4面体网格自由划分,所划分的网格足够小同样能保证结果精度。采用大型有限元前处理软件ANSA划分飞轮壳结构并利用ANSYS提供的空间实体单元SOLID185进行离散化。整个模型结构共划分了773239单元。
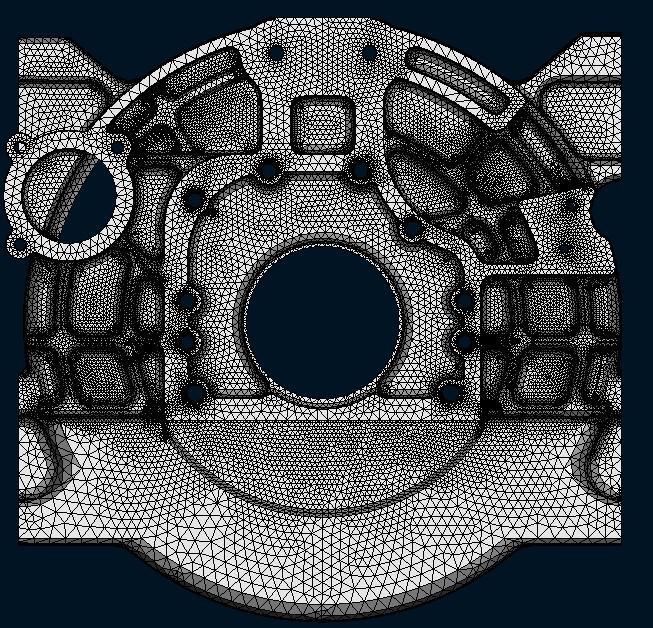
图2-1 飞轮壳结构三维有限元网格模型
3 飞轮壳-传动系施力下静力学分析结果
利用Ansys有限元分析,获得两种施力情况下5种工况时,结构部件的Von Mises应力云图。根据应力云图可以判断飞轮壳实际断裂发生位置的应力值大小。
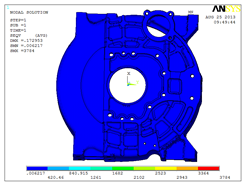
图3-1飞轮壳-发动机面整体应力云图
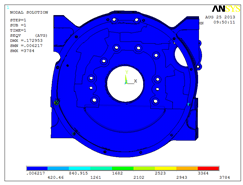
飞图3-2 飞轮壳-离合器面整体应力云图
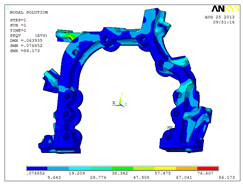
图3-3 飞轮壳-发动机连接端面部分应力云图
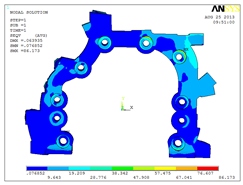
图3-4飞轮壳-发动机连接端面背面的应力云图
4 结果分析
(1)传动系传力
根据传动系传力的五种不同工况的有限元分析结果可知,飞轮壳结构的应力云图分布层次不明显。在刚性悬臂梁端的弯矩对于飞轮壳实际发生断裂的部位应力值小。集中应力主要发生与离合器相连接的螺孔处,该处与被全约束固定的左机座相对应。由此可认为,在传动系端发生的弯矩不易导致飞轮壳结构的断裂。
(2)机座传力
根据机座传力的五种不同工况的有限元分析结果可知,飞轮壳结构的应力云图分布层次较为明显。模拟结果应力较大的位置与飞轮壳实际断裂的位置较为相似。由此可认为,在机座处传力可导致飞轮壳结构的断裂。从表5-1中可知,机座传力工况5比较接近飞轮壳裂纹实际发生的位置。
机座传力下五种不同工况应力分布位置汇总
工况序号
| 应力值较大部位
| 备注
|
工况1
| B、C、E、F
| |
工况2
| A、B、C、D、F
| A处不十分明显
|
工况3
| A、B、C、D、F
| A处不十分明显,D处不如工况2中的明显
|
工况4
| B、C、D、E
| |
工况5
| A、B、C、D、E、F
| A处不十分明显
|