项目来源:福建省龙溪轴承(集团)股份有限公司 项目编号:
自润滑关节轴承改变了传统关节轴承的润滑维护方式,以其自润滑、免维护、摩擦系数低、耐冲击、结构紧凑、体积小、动载荷能力大、寿命长等优点,广泛应用于航空飞行器、风电、动车、重载铁路货车、载重汽车、高端工程机械、高端油缸及建筑钢结构节点等领域。其质量的好坏直接决定了工业技术的发展。本文分别研究关节轴承一次挤压成型和二次挤压成型的过程模拟。观察该轴承挤压变形过程和回弹过程,得出挤压过程中塑性成形的流动规律、内外圈接触压力分布情况和回弹后内外圈间隙分布情况。研究结果可为关节轴承工艺设计和生产提供新的技术依据。
1.轴承装配图及挤压模拟图
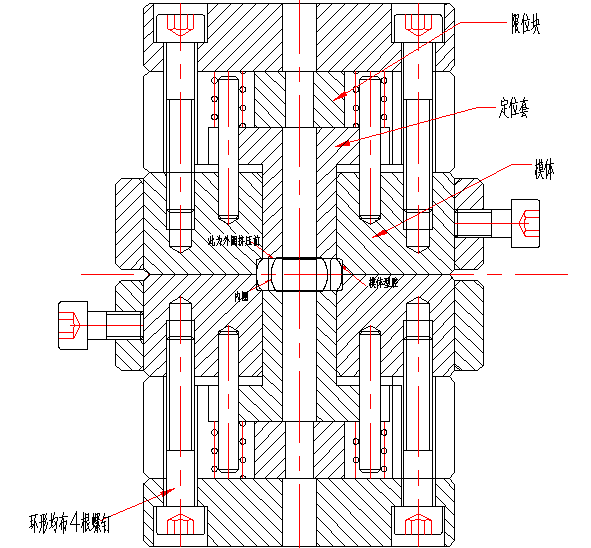
图1 轴承实际装配的模型示意图
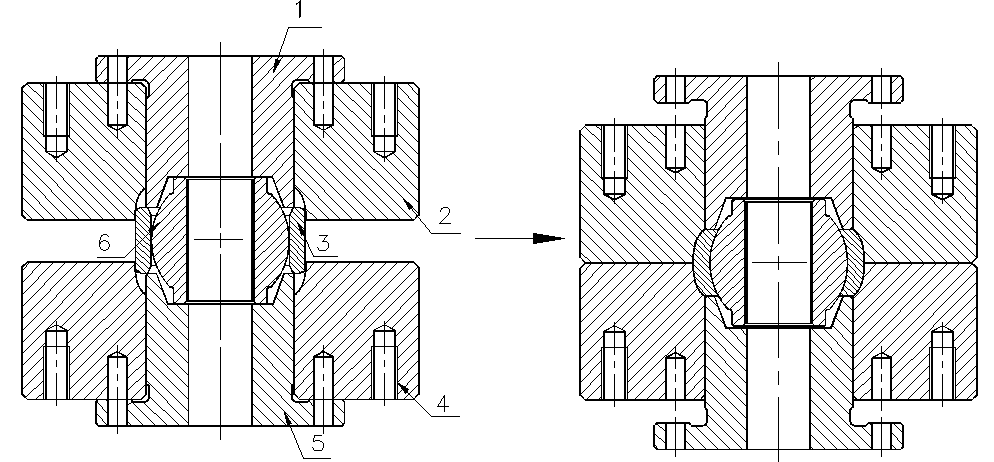
(a)挤压前 (b)挤压后
1-上定位套 2-上模 3-外圈 4-下模 5-下定位套 6-内圈
图2 轴承挤压原理图
2.关节轴承一次挤压成形过程模拟
1、轴承初始装配时,定位套对外套没有起到定位作用,设计定位套时,应该使其在初始装配时起到定位作用。根据金属流动最小阻力定律,应对定位套加工一半径为0.5mm-1mm圆角。
2、在挤压过程中所消耗的功率主要由三部分组成:①塑性变形消耗功率;②摩擦消耗功率;③速度间断消耗功率。故在挤压过程中要尽量保证模具下压速度均匀并尽量减小接触面之间的摩擦系数。
3、整体卸载之后,轴承外圈两端会有较大的回弹量,为了减小回弹量可以适当采用回弹补偿法,即在出口处适当增加曲率半径。
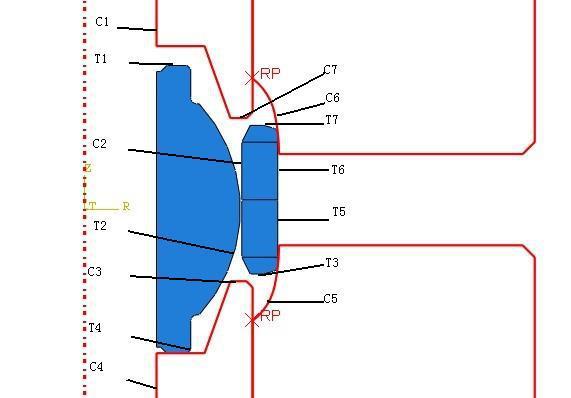
图3 七个接触对示意图
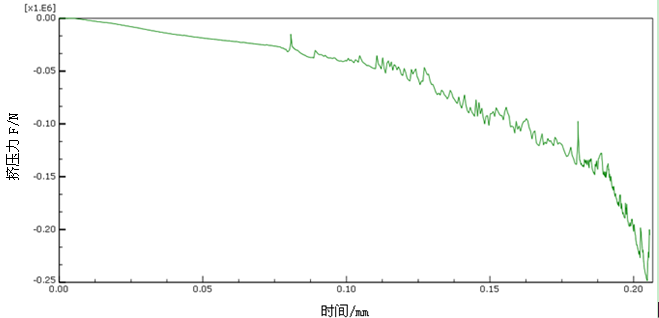
图4 挤压力曲线
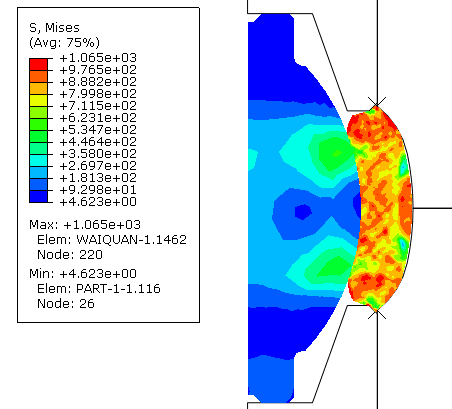
图5 挤压完成后轴承内外圈Von Mises等效应力云图
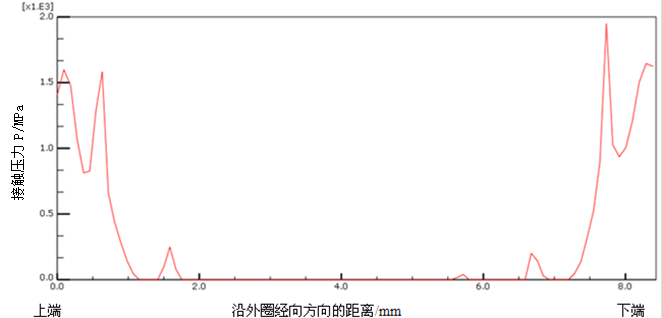
图6 轴承内外圈之间的法向接触压力
3关节轴承二次挤压成型过程模拟
1、第一次成形装配时,定位套对外圈没有起到定位作用,导致外圈两端出现了剧烈的变形。设计定位套时,应该使其在初始装配时起到定位作用。根据金属流动最小阻力定律,应对定位套加工半径为0.5mm-1mm的圆角。
2、在挤压过程中所消耗的功率主要由三部分组成:①塑性变形消耗功率;②摩擦消耗功率;③速度间断消耗功率。故在挤压过程中要尽量保证模具下压速度均匀并尽量减小接触面之间的摩擦系数。
3、从第一次挤压结果可以看出,成型模具的圆弧曲率可以相对增大,定径带长度可以减小。第二次成型模具在出口处适当增加曲率半径,以补偿回弹量。
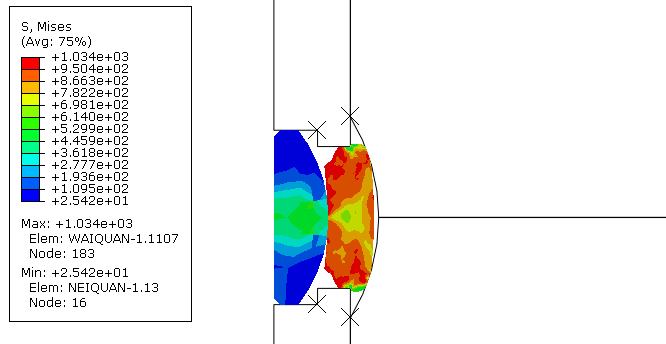
图7 一次成型挤压完成后轴承内外圈Von Mises等效应力云图
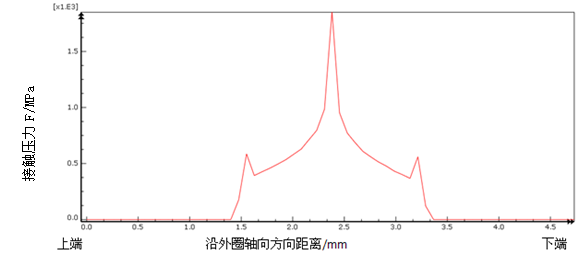
图8 一次成型轴承内外圈之间的法向接触压力

图9 二次成型挤压完成后轴承内外圈Von Mises等效应力云图
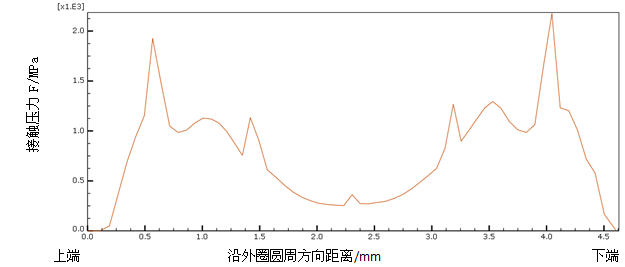
图10 二次成型轴承内外圈之间的法向接触压力