项目来源: 项目编号:
在用含缺陷压力容器和压力管道对安全生产形成了严重威胁,成为企业最大的隐患。然而一味强调安全,而盲目地将所有含缺陷压力容器和压力管道作返修或退役处理也是不现实的。事实上,有些缺陷在一定的环境条件下并不影响压力容器和压力管道的安全使用。因此正确评价一个己知缺陷的危害性,确定含缺陷结构的安全裕度,是一个与整个生产系统的安全性和经济性直接相关联的重要问题。
本研究结合漳州华阳电业有限公司后石电厂600MW超临界发电锅炉中三通管座出现大量的裂纹、未熔合缺陷的工程实例,以承受内压作用的焊制三通管座为研究对象找出产生三通管座缺陷的原因;分析在缺陷存在的状况下,三通管座的剩余寿命;探索解决的方法,提出延长使用寿命的方向;为今后设计的改进、加工工艺的完善打下基础。
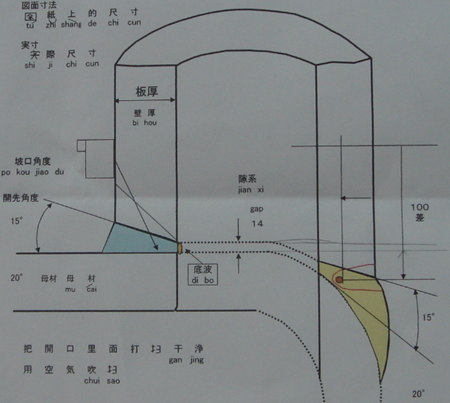
a、三通管座结构实物 b、三通管座结构示意图
1.三通管座结构及实测缺陷分析
据统计每台600MW发电锅炉内共有92个规格大小不同的三通管座,福建省锅炉压力容器检验所在近几年定期检验中在三通管座焊缝内部检出了大量的裂纹,对检出裂纹缺陷的焊缝进行收集整理。
2.无缺陷三通管座模型数值分析
三通管座实际是主管道与支管道的相贯体,由于其在相贯区域的周围几何结构存在薄膜不连续性,使其在相贯线周围产生较大的应力集中。其通常是系统强度的薄弱点,往往成为灾难性事故的原发点,因此其强度能否满足使用要求关系到整个系统能否正常安全的运行,由于其影响参数众多,对其强度进行精确可靠的理论计算至今尚难以做到,鉴于上述情况本研究利用有限单元法原理,应用ANSYS结构分析程序,对已检出缺陷的三通管座进行不含缺陷时结构强度的精确计算。
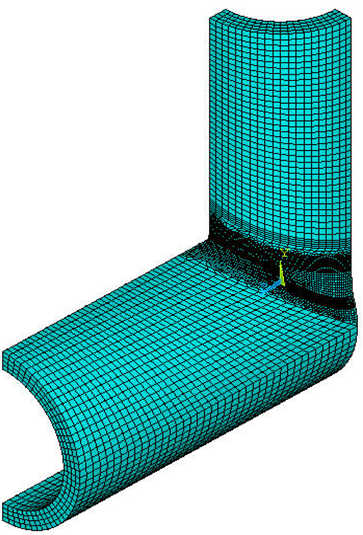
计算模型单元网格图
整个模型应力强度分布云纹图
3.三通管座应力实验验证分析
为了验证有限元法计算结果的可靠性、正确性以及准确程度将已经计算的有限元模型与光弹实验测试结果进行比对验证,由于考虑到光弹实验模型在实际制作过程中的难度程度,在光弹实验模型制作中忽略了焊接三通管座的焊缝结构,为了较好的比对我们采用原先有限元建模过程中同样的方法步骤重新建立光弹试验模型的有限元模型,在这次建模中同样也忽略三通管座中的焊缝结构,以使得有限元模型与光弹实验模型一致。
经ANSYS有限元结构分析程序计算得到结果如下。
(1)、在Φ830×85/Φ762×85mm三通管座有限元模型中远离边缘区域主管内壁面周向应力计算值为24.218Mpa,外壁面周向应力计算值为18.274Mpa,与光弹实验模型对应点处应力测试值比较,误差分别为3.13%和3.84%。说明两者间相符程度很好。
(2)、在三通管道肩部内拐点处应力强度值为103.5Mpa,腹部外表面最大应力强度值为84.7Mpa,与光弹实验模型对应点处应力强度比较,误差分别为39.86%和28.3%。两者误差较大,分析误差的原因,首先有限元计算给出的应力强度值是某点处最大应力强度值,而光弹实验给出是某点处某个方向的应力强度值,两者显然会有所偏差。其次光弹模型实验值的测取是通过切片来达到的,切片的厚度将影响到测试数值的大小,尤其在该高应力变化梯度的区域。另外光弹模型制作整个过程由手工完成肯定会存在一定的偏差。
4.含缺陷三通管座模型数值分析
由断裂力学的理论知道,在裂纹尖端附近的应力场具有奇异性,即在靠近裂纹尖端的各应力分量均与K/r1/2成正比。由此可见,当r趋于0时,应力急剧增长。在有限元法中,通常在有限尺寸的单元中用多项式表示位移,因此在奇异点附近不能很好的反映应力的变化。为了克服这种不足,目前在有限元中通常采用两种方式解决,一种是在裂纹尖端附近把网格划得很细,这种方法难度较小,较容易建立计算模型,而被广泛采用,但计算误差相对较大。另一种方法是在裂纹尖端处采用特殊的奇异单元,由于这种方法建立有限元计算模型难度较大,因此目前这种方法在有限元计算中采用的不多,尤其是在三维结构中其难度更大,但该方法能很好、且较准确模拟裂纹尖端附近应力场的奇异性,而计算得到的应力强度因子误差较小,更接近实际状况。因此本研究采用后一种方法计算三通管座缺陷的断裂因子。
5.含缺陷三通管座主要工作及结果
(1)、应用结构相似原理和量刚分析法分析存在缺陷的89个三通管座几何尺寸及结构特点,得出可用3个特征参数(三通管座的内径比、厚度比及开孔系数)予以表征,当三通管座特征参数相等时结构是相似的,因此这些含缺陷的三通管座可用20组参数所涵盖,缩小了研究的分散性。
(2)、应用数值分析方法,采用ANSYS结构分析程序对不存在缺陷的三通管座进行了强度计算和疲劳分析,得出了三通管座在其主要载荷——内压力作用下,应力强度分布特点、最大应力强度产生的位置和数值,并应用数值处理方法对计算所得的应力强度进行分解。
(3)、通过对日本三菱重工株式会社对三通管座设计依据的分析,比较了国内外相关标准对开孔接管有关章节条款的要求和限定条件,发现ASME B31.1-2004,压力管道规范——动力管道中壁厚的设计采用中径近似计算公式,也未对其适用范围加以限制,将三向应力简化为二维应力处理,忽略了在高压力下产生的不可忽视的径向应力的影响,产生了较大的计算误差,造成部分三通管座总体薄膜应力超出了材料的许用值。其次该标准中对三通的开孔接管强度计算模型采用的是无限大平板开小孔,忽略了圆柱壳曲率半径的影响,在补强量计算中采用等面积补强,这种模型仅适合于开小孔,即内径比小于0.5的情况,对于三通管座中内径比远大于此的结构,其计算误差较大,幸好三菱重工在设计中未严格按照要求取临界值,而采取加大补强量的方法弥补设计方法的不足。
(4)、应用光弹实验测量、电阻应变测试技术以及理论计算方法验证有限元计算结果,比较结果表明有限元在建模、网格划分、单元的选取、载荷的处理、边界的简化是正确的,反映了结构的实际状况,计算结果是准确的、可信的,其精度满足工程的需要,这为后续研究奠定了基础。
(5)、应用断裂力学原理,参照GB/T19624-2004,在用含缺陷压力容器安全评定标准中相关方法对检出的面型缺陷进行规则化处理和表征,将不规则的缺陷整理成适合分析的椭圆形埋藏缺陷、半椭圆形表面缺陷以及穿透的矩形缺陷。在处理过程中充分考虑裂纹间相互干涉影响的因素,使分析有代表性,也更基于安全。这种做法是目前断裂力学分析实际结构缺陷的常规方法,也是相关标准广泛采用的基本方法。
(6)、在三通管座实际结构中,采用三维模拟三通管座缺陷状况,并采用了高精度的20节点三维奇异退化体单元,分析计算了结构应力强度因子,得到了结构含有缺陷情况下最大的应力强度因子。目前三维模拟实际结构缺陷状况是有限元方法解决实际问题的一个难点,且相关报道很少,尤其是在三维有限元分析中采用奇异单元,很好的模拟了裂纹前缘区域的应力场和位移场,使分析精度大大提高,这比日本三菱重工株式会社做的简单拉伸情况下的断裂力学分析前进了一大步。所得出结果也与其大相径庭,并不是所有检出含有缺陷的三通管座都是安全的,也不像三菱给出的结果:含缺陷的三通管座还可以安全使用十万小时以上。
(7)、为了进一步了解在三通管座在简单的载荷——内压力下,就会产生复杂应力分布的这样一个特定结构,应用正交实验法科学安排应力强度因子影响因素,通过对三通管座应力强度因子变化情况的比较分析得出应力强度因子的变化趋势,三通管座外表面或者浅外表面缺陷应力强度因子较大,也是比较危险的;腹部处的缺陷较其它位置的缺陷更易于扩展;由于三通管座本身结构受力的特殊性,缺陷尺寸大小对应力强度因子的影响与裂尖所处位置的应力强度大小有关,但不是简单的增大或减小。
(8)、研究表明:现有检出的缺陷不是由于三通结构强度不足引起的,缺陷起因在加工制造过程中,三通管座原有的缺陷在使用中在特定的载荷状态下得到了发展,因此应调查了解三通管座加工制作工艺,根据目前焊接技术水平像三通管座如此厚度的结构,采用人工焊接是不大可能的,若采用机械埋弧电渣焊制作工艺,焊缝组织晶粒较粗大,多有偏析现象,若未能做到焊后层层热处理,其极有可能成为裂纹的诱发点。